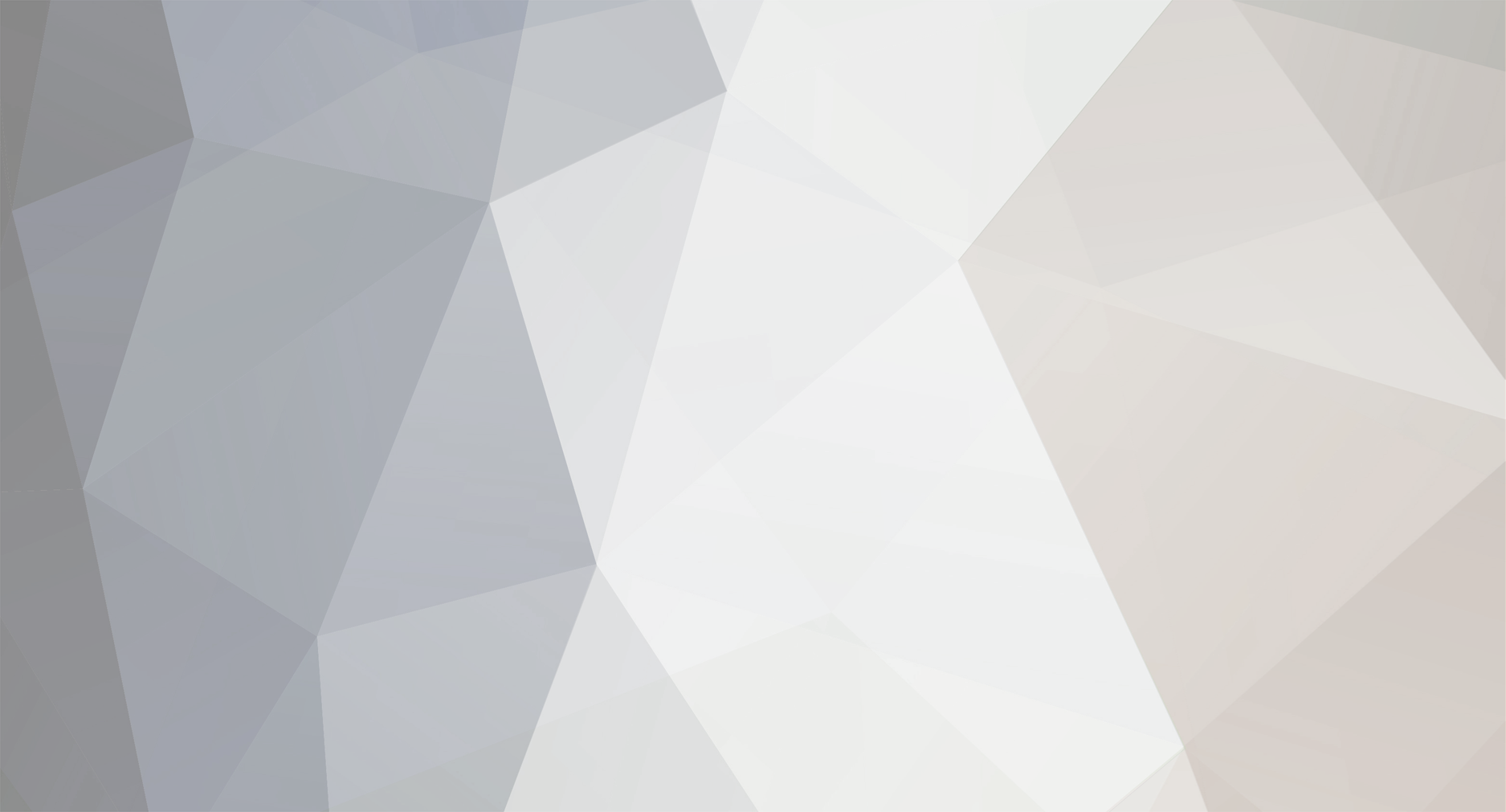
Smith2007
ПРОФИ-
Публикации
185 -
Зарегистрирован
-
Посещение
-
Дней в лидерах
13
Последний раз Smith2007 выиграл 26 июня 2022
Публикации Smith2007 были самыми популярными!
Репутация
69 ПРОФИО Smith2007
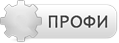
-
Звание
Ветеран
- День рождения 01.01.1967
Дополнительная информация
-
Пол
Мужской
-
Город
Стерлитамак
-
Деятельность
Хобби
-
Оборудование
СО2 Лазер, CNC Фрезер
Посетители профиля
Блок посетителей профиля отключен и не будет отображаться другим пользователям
-
Какой-то глюк на форуме. Вдруг фото продублировалось 3 раза. Поправьте если возможно. Мне уже не дает редактировать. Линзы на станке меняются часто. В зависимости от задачи. С фокусом от 73мм до 420мм. Сам датчик планирую разместить таким образом, что бы его ось совпадала точно с красным лучом. Ось лазера. Датчик будет выдвижным на штанге.
- 29 ответов
-
- ось z
- волоконный маркер
- (и ещё 3)
-
На очереди автофокус. Застопорился на выборе датчика. Точнее на диапазоне измеряемых расстояний. Из того, что доступно на алике это: 65-135 мм (погрешность 0,1мм) 200-600 мм (погрешность 0,8 мм) Пока склоняюсь к первому. Хотя не очень удобно при работе с линзой F315 мм Что думаете?
- 29 ответов
-
- ось z
- волоконный маркер
- (и ещё 3)
-
Приехал клапан и редуктор. Подключил, обновил прошивку.
- 29 ответов
-
- 1
-
-
- ось z
- волоконный маркер
- (и ещё 3)
-
А это сам код. Нижняя строка не используется. Это прообраз будущей 3Д обработки
- 29 ответов
-
- ось z
- волоконный маркер
- (и ещё 3)
-
Проект получил неожиданное продолжение. В процессе работы, бывают довольно длинные задания. Иной раз доходят до 40 минут. Безусловно сидеть на против станка и пялится на блуждающий огонек нет ни какого смысла. Можно заняться более продуктивным времяпровождением. При работе станка всегда включаю вытяжку, а иногда и дополнительное воздушное охлаждение заготовки. И вот уже не первый раз, когда после завершения задания я не сразу подхожу к станку, особенно если нахожусь в соседнем помещении. Но вытяжка продолжает молотить, компрессор накачивающий воздух продолжает качать воздух. В общем давно уже меня это не устраивало и все дума как бы сей процесс автоматизировать. Началось изучение возможностей контроллера управления маркером На разъеме DB15 нашел программируемые входы и выходы В настройках EzCad2 можно их сконфигурировать на вывод сигналов. Ну а далее завел эти сигналы на ПЛК, дописал 4 строки кода и задача решена! Для управления нагрузкой 220В - использовал твердотельное реле . Вот что получилось Меня не покидает желание запустить 3Д гравировку. Среди плагинов нашел "Гравировка по событию". В первом приближении это может помочь. Но я не смог с ним до конца разобраться. Так же в EzCad2 пристутствует пункт "Нарезка stl модели на слои". Но я так же не смог с ней разобраться как она работает либо у меня просто не подходящая версия EzCad 2.7.6. Предположим, что мы нарежем STL на слои с шагом 1 мм. Полученные вектора выгрузим в dxf и на их основе сформируем задания для маркера. По каждому слою задание сохраняем в отдельные файлы. Затем запускаем обработку первого файла и ждем окончания цикла. По окончании опускам Z на 1мм ниже (или на ту величину с которой нарезали stl) и запускаем следующий файл. И так далее. В идеале конечно это написать свой плагин для этого, но по предварительной информацией для этого потребуется не 1 тыс зеленых денег, что меня несколько огорчило. Может есть у кого идеи на этот счет?
- 29 ответов
-
- 1
-
-
- ось z
- волоконный маркер
- (и ещё 3)
-
Выбор станка для резки фанеры и нержавейки?
Smith2007 ответил в тему пользователя Алмаз1980 в Что выбрать?
На такой объем нет смысла в станке. Согласен. Гораздо проще раз в месяц отправить на резку в компанию, что имеет соответствующее оборудование. Это будет наиболее эффективно. зы. это мое личное мнение.- 13 ответов
-
- резка металла
- металлообработка
- (и ещё 3)
-
Выбор станка для резки фанеры и нержавейки?
Smith2007 ответил в тему пользователя Алмаз1980 в Что выбрать?
Вы серьезно? Но даже если это правда - 10 мм/сек - это слезы. И нержавка - это не чернуха и режется гораздо труднее. Если есть задача резать металл - нужно станок для резки металла. Я придерживаюсь такого мнения. В конечном счете цель - заработать. Но как можно зарабатывать когда у Вас себестоимость работы запредельная?- 13 ответов
-
- резка металла
- металлообработка
- (и ещё 3)
-
Выбор станка для резки фанеры и нержавейки?
Smith2007 ответил в тему пользователя Алмаз1980 в Что выбрать?
Вам нужно 2 разных станка. Для резки неметаллов СО2 лазер. Для резки нержавки - волоконный лазер (1064 нм) И не верьте тем, кто говорит, что на СО2 можно резать металл. Себестоимость такого реза будет запредельной и не конкурентной даже близко к волоконным лазерам. Что бы резать с приемлемой скоростью 1 мм нержавки - достаточно 1 кВт лазера. зы. Сталь3 до 5мм можно порезать на 1 кВт в кислородной среде. Нержавку резать лучше в азотной среде.- 13 ответов
-
- резка металла
- металлообработка
- (и ещё 3)
-
Дополню по опыту эксплуатации: Распределители бронзовые текут. При чем перепробовал разные. Все текут. Поставил краник как Павел приводил ссылку. Держит 3ий месяц. За время эксплуатации с апреля масло еще не доливал в бак. Примерно раз в 2 недели протираю направляющие от излишков масла. Вывод: Все получилось. Со смазкой теперь полный порядок.
- 9 ответов
-
- направляющие
- масло
- (и ещё 5)
-
Фрезер дергался сильно. Не понимал причину. Просто обнулил стартовую скорость. Стал плавно работать. Не думаю, что это сильно на производительность повлияет. Ускорения достаточно высокие. Так же и в этом случае, возможно поможет. Хотя у меня гибриды.
- 98 ответов
-
- не совпадение
- не состыковка
- (и ещё 3)
-
Вот еще можно попробовать. Но все же я больше склоняюсь к дефектным шкивам
- 98 ответов
-
- 1
-
-
- не совпадение
- не состыковка
- (и ещё 3)
-
Это что за дробление такое? При очень малых микрошагах, крутящего момента может просто не хватить преодолеть трение в кинематике. Или там сервошаговые?
- 98 ответов
-
- не совпадение
- не состыковка
- (и ещё 3)
-
Меня одного смущает это значение? Как его определили? Если автор уверяет, что геометрия станка норм, то эти значения нужно вычислить. Кроме того заявление о том, что в разных местах поля по разному ошибка проявляется - говорит все же о кривом портале. В 2Д можно проверить самим станком. Но нужны инструменты, что бы проверить параллельность направляющих. Я бы по сделал импульсы на фанере в точках прямоугольника с максимально возможными размерами (по размеру поля) и замерил диагонали. Сравнил их с вычисленными математически. Что касается значения "длина шага": Вычислить. ШД скорее всего 200 импульсов на оборот. Далее смотрим редуктор. Передаточное отношение можно посчитать по количеству зубьев. Умножить это все на дробление шага и рассчитать.
- 98 ответов
-
- не совпадение
- не состыковка
- (и ещё 3)
-
Думаю не проще. Как минимум нужно было писать какой-то графический интерфейс, разбираться с форматом команд на модбас или uart. Я посчитал это лишней тратой времени. Тут все готовое. Только алгоритм дописать. Хотя возможно есть полноценные эмуляторы этих панелей. Я просто не интересовался.
- 29 ответов
-
- ось z
- волоконный маркер
- (и ещё 3)
-
видосик
- 29 ответов
-
- 2
-
-
-
- ось z
- волоконный маркер
- (и ещё 3)